§1. Short information The main tasks of hardware and software include the following:
- automation of test preparation process and a test configuration;
- automation of a metrological verification process and measuring channel calibration;
- maintaining of technological database with testing datas attributable to tested node, to sensors used, to individual calibration curves used;
- automation of a parameters registration with given sequence diagramm and with given sampling rate;
- data visualization in real-time mode on a chief dash-board display;
- real time control of bench's equipment using predefined algorithms;
- postprocessing of test results.
§2. Function Permanent improvement of aerospace complex products, modern tempos and technologies of new items development and application dictate new demands to experimental base of production existing, which as often comes turns into a critical link in the process.
The number of monitored and adjustable parameters enlarges, the demands to metrological characteristics of measuring channels increase, sample rates raise as well, results processing methods get complicated. The new demands to test preparation efficiency, maximization of a range of goods being tested, time of new tests mastering are made.
Laboriousness of a periodical metrological check-up and channels approval as well as standstill during verification period come unacceptable.
Everything abovementioned is leading to the necessity of automation means usage on testing desks, development and application of hardware and software complexes of automated systems of desk tests technological process control on the base of computer aids wide application.
As a solution of the above-listed problems RTS-Soft offers a complex of firmware solutions on RTOS QNX base, Advantech company technics and our own software. To basic tasks of hardware-software complex one can refer the following:
- automation of a test preparation and configuration process;
- automation of a metrological verification process and measuring channel calibration;
- technological database of test results maintenance with data fixation on goods, data fixation on sensors and own calibration;
- automation of a parameters registration process on programmed mission profile with programmed frequency;
- data visualization in real -time mode on a chief board display;
- real time control of stand equipment on algorithm given;
- postprocessing of test results
§3. The history of creation The first system being created to solve assigned tasks was developed and applied on test desks of the State Design Office 'Juzhnoyje' enterprise called after Jangel in 1999. At first it was assigned for test automation on one desk and for the goods of a certain type (liquid-propeller rocket). But then it was developed for different goods types and applied on one more desk assigned for solid-propeller rocket engine tests pass. The system is functioning under RTOS QNX 4.25. The choice of that operational system as a base allowed to meet a wide array of demands being raised to systems of such type namely: data collection reliability and guaranteed time of executive instructions playback. Not only success of a test pass but often desk staff lives depend on fulfillment of these crucial demands. This system has been still in active use.
In 2004 the development of a new hardware and software complex was started for the purpose of application of more flexible and universal test settings interface and increase of data collection reliability and control algorithms.
Experience having been received while complex data development allowed to create an independent commercial software product named 'Octavo'. It was created taking into account previous systems and it represents unique environment for setting and passing any type of tests on the goods produced. As a base OS we use RTOS QNX 6.2. §4. Basic options and characteristics To basic characteristics of this system one may refer following options:
- Registration of parameters with frequency 1000 Hz;
- Registration of pressure potentiometers parameters, atrain meters vacuum parameters, frequency meters rod, rotation (25…500 Hz) of frequency pressure meters, thermistor (TH 50\100 Ohm) force (3…20 KHz) of thermocouples XK and XA;
- Registration of discreet channels of current (0…32V) voltage input;
- conducting a procedure of sensors calibration with return and calibration result preservation and linearization coefficient calculation;
- an option of addition to a system of optional type sensors;
- an option of conducting a procedure of metrological system attestation with return;
- test results processing and return by way of reports and graphs;
- an option of discreet control instruction issue on mission profile with 1 millisecond resolution;
- -'Octavo' system is applied using Java technology and bases on plug- in option conception therefore it can be easily expanded for a particular customer`s needs;
- an option of an arbitrary control algorithm addition to a system (e.g. automatic control of fuel delivery consumption, chamber swaying and so on);
- an option of creating of provider symbolic circuits and of data drawing;
- an option of access to registered data through ODBC interface;
- record of provider`s actions;
- -'Octavo' system is applied using Java technology and bases on plug- in option conception therefore it can be easily expanded for a particular customer`s needs.
§5. Program interface drawings 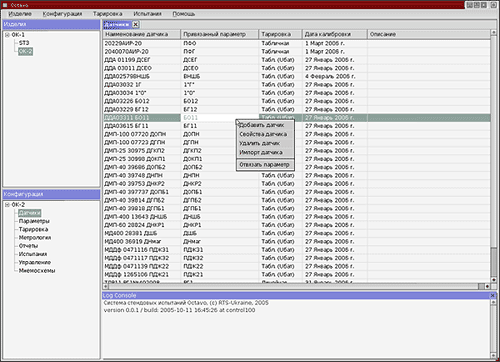 | Drawing 1. A box of product configuration: a view of a sensors editor |
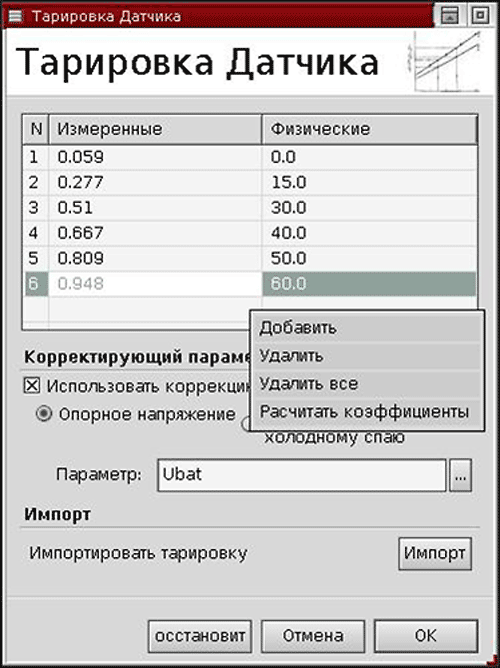 | Рисунок 2. Диалог редактирования тарировочной таблицы датчика |
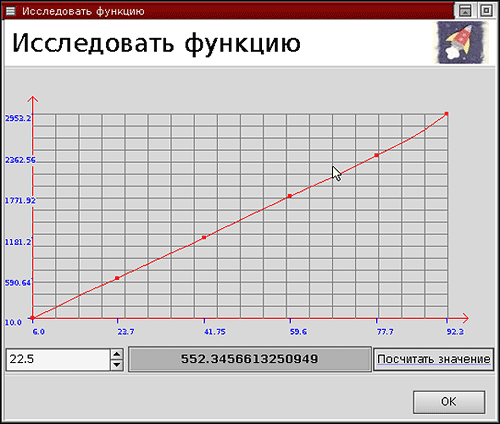 | Рисунок 3. Окно исследования аппроксимирующей функции |
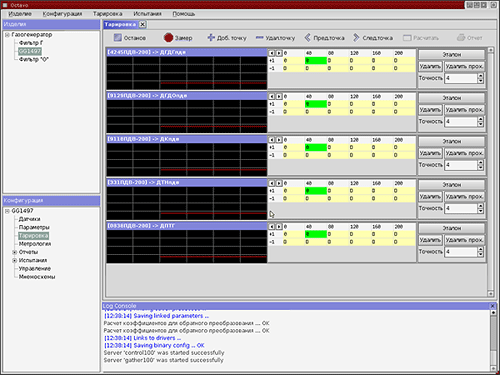 | Рисунок 4. Окно конфигурации изделия: с открытым видом менеджера тарировочной процедуры |
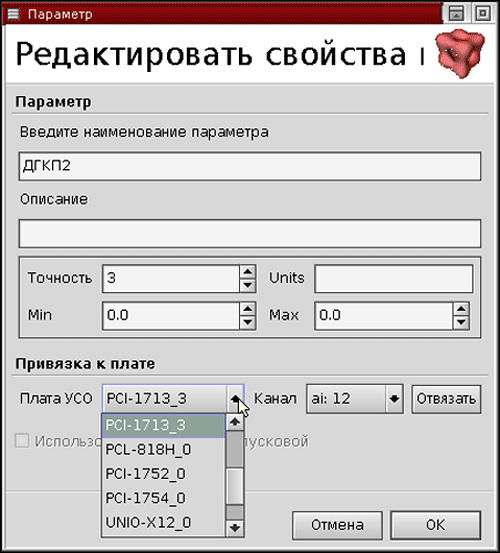 | Рисунок 5. Диалог редактирования свойств параметра |
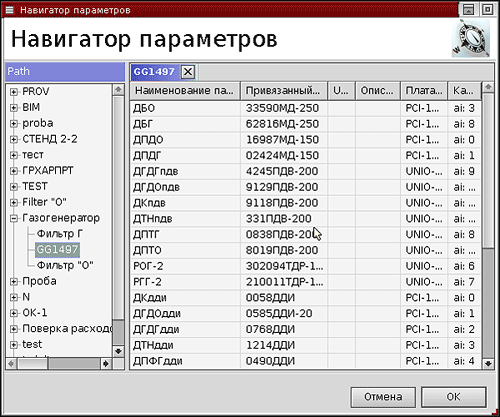 | Рисунок 6. Окно навигатора параметров по всем изделиям и конфигурациям |
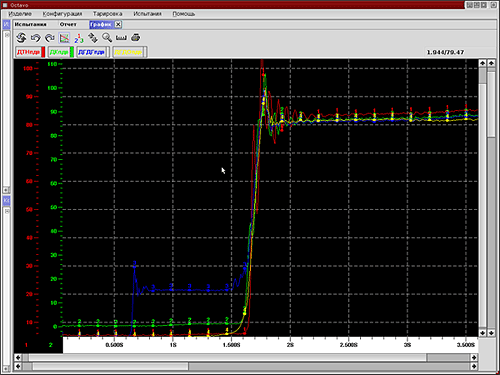 | Рисунок 7. Просмотр результатов испытания: вид просмотрщика графиков |
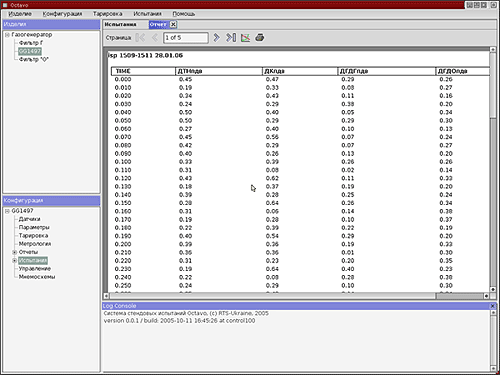 | Рисунок 8. Просмотр результатов испытания: вид просмотрщика сформированных отчетных форм |
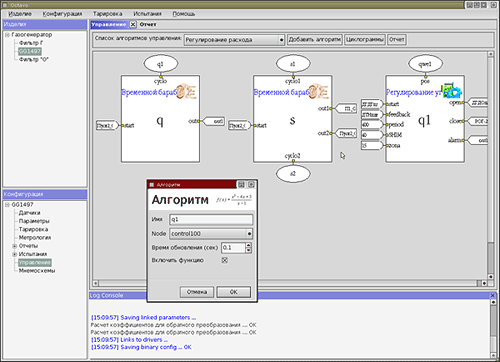 | Рисунок 9. Окно конфигурации изделия: вид редактора алгоритмов управления с диалогом добавления нового алгоритма |
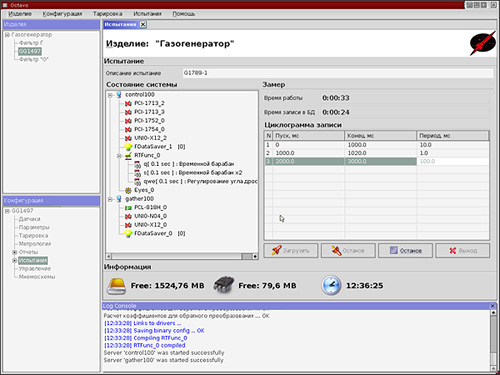 | Drawing 10. A view of the test conducting manager – a representation and control of a test course. |
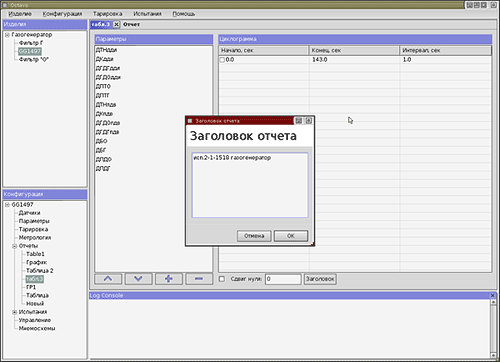 | Рисунок 11. Окно конфигурации изделия: вид построителя отчетных форм |
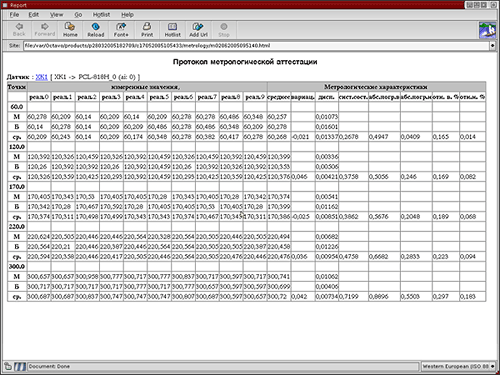 | Рисунок 12. Протокол результатов метрологической аттестации в html-браузере |
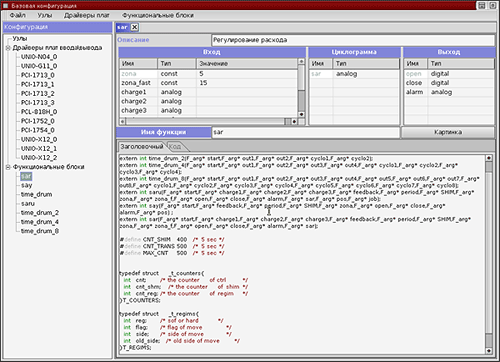 | Рисунок 13. Вид редактора алгоритмов управления доступен администратору системы |
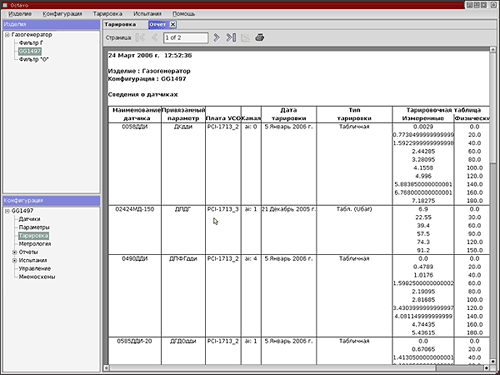 | Рисунок 14. Отчет по изделию в целом датчики, параметры, тарировочные характеристики и т.д. |
|